Today’s challenge to increase productivity with fewer resources has lead to numerous methodologies and toolkits to help organizations meet their objectives and become more profitable and effective. This certainly makes the case for applying two well known and proven methodologies Business Process Management (BPM) and Six Sigma.
June 22, 2006
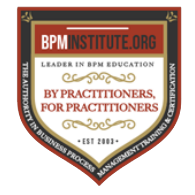
Marvin Wurtzel
Business Process Management (BPM)
Articles by: Marvin Wurtzel
Successful Six Sigma Deployment
The vast majority of Six Sigma proponents agree to the fact that the key to Six Sigma improvement success is the building up of an effective infrastructure. An effective infrastructure is the foundation for the success of the organization in its implementation of Six Sigma. It is also clear that the success of Six Sigma lays on the projects selected and their link to the strategy of their organization and the effectiveness of the value chain processes.
Reasons for Six Sigma Deployment Failures
As a Six Sigma consultant I am often asked: “Have there been any Six Sigma deployments that have failed?” My answer is ambiguous enough to make me sound like a presidential candidate. That answer depends on your definition of the term “failure.” My definition of a failure would be a result that does not deliver the Return On Investment (ROI) anticipated by the company. Using this definition, I am not aware of any company that would admit to failed deployment.
Integrating Lean and Six Sigma
Both the Lean and the Six Sigma methodologies have proven that it is possible to achieve dramatic improvements in cost, quality, and time by focusing on process improvement. Six Sigma is focused on reducing variation and improving process yield by following a problem-solving approach using statistical tools, Lean is primarily concerned with eliminating waste and improving flow by following the Lean principles and a defined approach to implement each of these principles.
The Marriage of BPM and Six Sigma
BPM Six Sigma Context
BPM tends to focus on the automation of business process through the use of BPM suites. Every software system automates a process; and generally every process, efficiency, or quality improvement project involves use of software systems.
Process Centric
“It’s all about process” – As stated by Jack Welch, General Electric’s famous CEO, success in business is all about process.
The Big Six Sigma Myths
Six Sigma has an attractive value proposition. Increase profits and improve customer satisfaction through more effective and efficient business processes. What company could say no to this idea? But, the Six Sigma methodology often is associated with daunting myths that prevent companies from taking advantage of its potential. For example, it’s assumed that Six Sigma is strictly for manufacturing processes, doesn’t work with Business Process Management (BPM).
Six Sigma – For All of Us
The popularity of Six Sigma continues to increase within large corporations as a means of improving quality and reducing costs. As most readers will know by now, Six Sigma has been adopted by leading corporations such as GE, Sun Microsystems, Allied Signal, Bank of America, Motorola, etc.
In the current business environment, IT organizations have been less passionate in adopting Six Sigma methods. Many organizations feel that they can’t afford the luxury of a Six Sigma Program. There is a feeling that it intended for the product or service areas of the business.
Can Six Sigma and Business Process Management Co-Exist?
One of the most powerful ways to improve business performance is combining business process management (BPM) strategies with Six Sigma strategies. BPM strategies emphasize process improvements and automation to drive performance, while Six Sigma uses statistical analysis to drive quality improvements. The two strategies are not mutually exclusive, however, and some savvy companies have discovered that combining BPM and Six Sigma can create dramatic results.
Creating a Customer Focused – Process Enabled Enterprise By Applying Business Process Management and Six Sigma Together
Creating a Customer focused – Process Enabled Enterprise requires a business process framework, established enterprise architecture, creating “real-time” business intelligence, and a link between continuous improvement projects and key business processes. Most businesses need to evolve from a bottoms-up Six Sigma (DMAIC) approach, to a strategic framework that will set the foundation for growth, accountability, and performance management.